Manufacturing
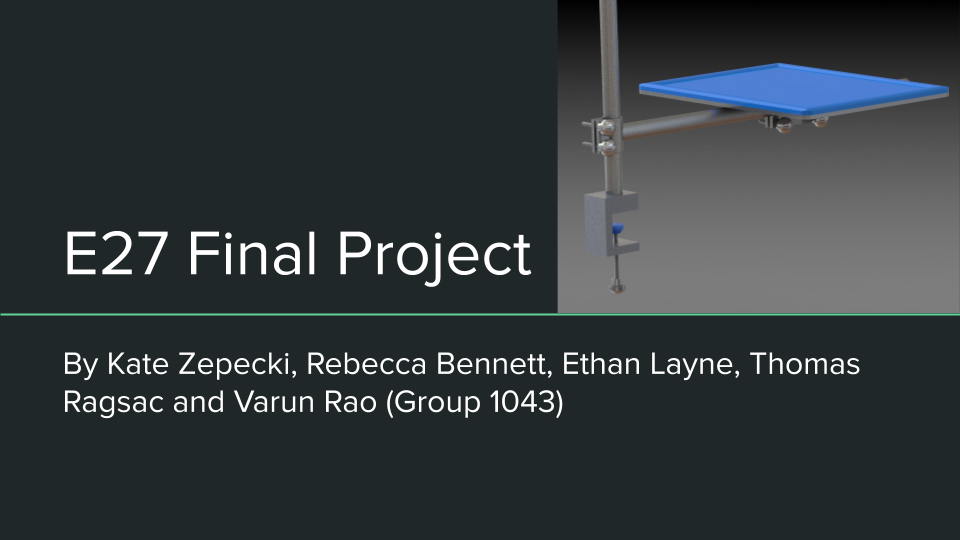
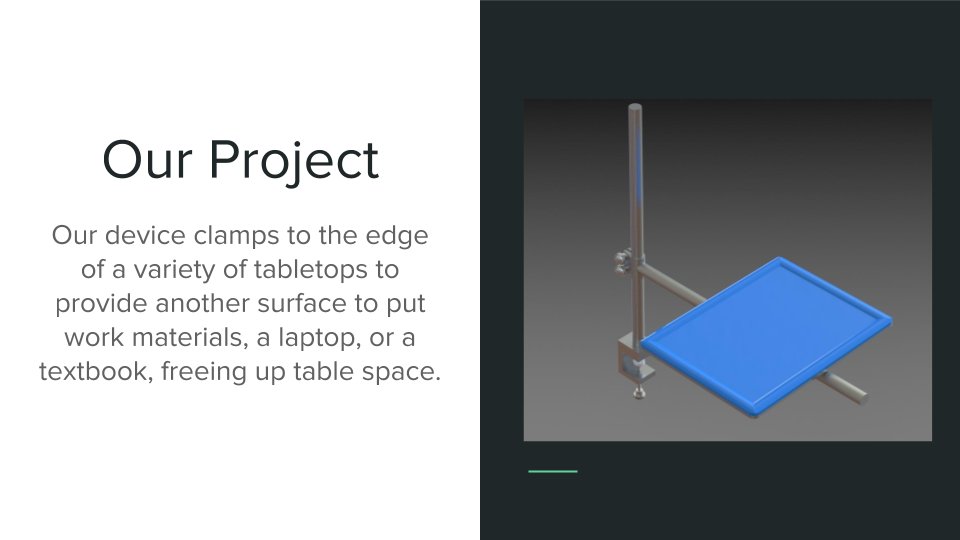

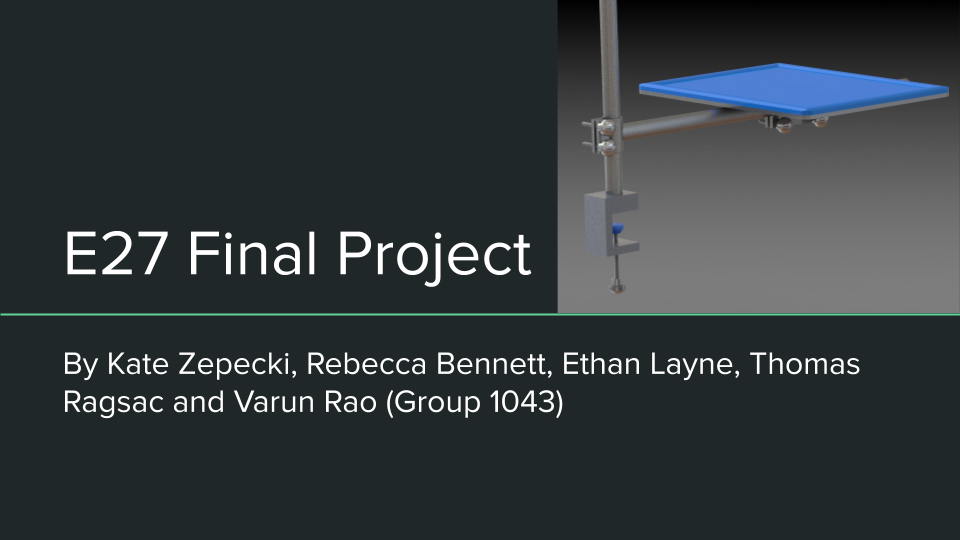
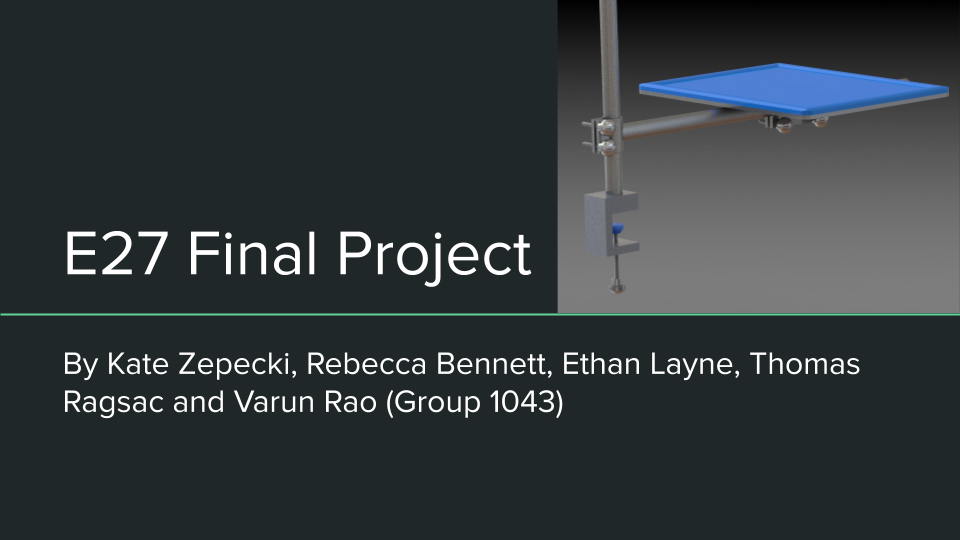


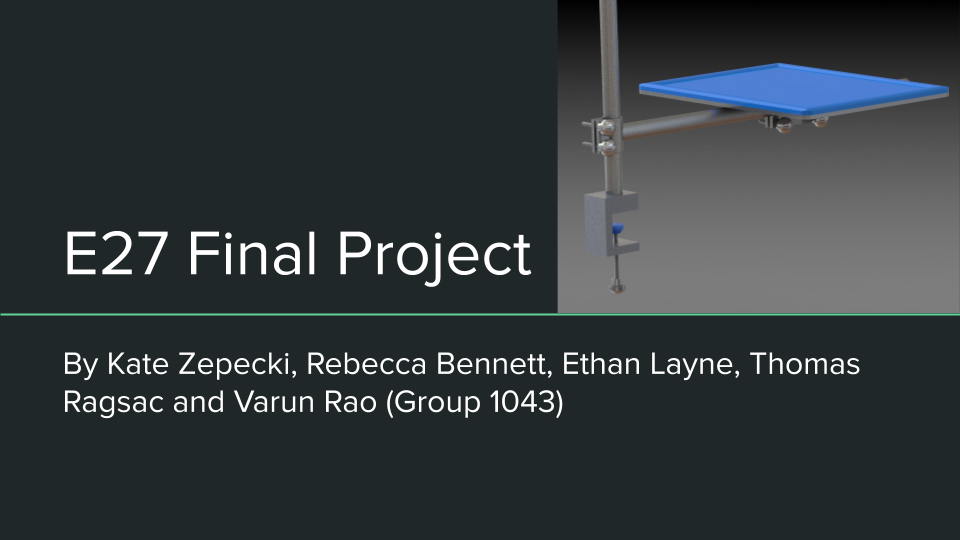
Skills learned:
-
Teamwork and communication in an online setting due to Covid-19
-
Referencing the Machinery's Handbook to decide fits, tolerances, and grades for a specific part
-
Referencing the Machinery's Handbook to decide appropriate manufacturing processes based on the grade for a part
-
Determining process selections for high volume manufacturing
-
Utilizing each person's unique skills and interests to design a product
The Goal of The Project:
To design a product that mounts onto an external object, in addition to being practice for specifying fits, tolerances, grades, and drafting engineering drawings using SolidWorks. In addition, my team was expected to use our specified tolerances and what we learned about high volume manufacturing.
Reflection:
It is amazing to see what my project mates and I achieved during a semester with Covid-19. I am grateful to have been able to work on a project with teammates who were understanding of each other's personal situations with Covid-19. Without everyone's effort, the final product would not be what it is now.
I am glad to have team members who were all skilled in certain areas where I was not and for my team members to be patient enough with me to practice new skills. While some of the members created CAD drawings and the engineering drawings, I was the one who referenced the machinery handbook to specify tolerances and double-check compatible manufacturing methods. The graduate student instructor and professor's advice was also very helpful when we could not progress. I do not know what we would do without digital tools like Zoom, Facebook Messenger, Google Drive, and GrabCad.
In the end, we were able to have a final product with engineering drawings (exploded, detail, and layout), parts with specified fits and tolerances, and manufacturing processes and material selections for each part.
Tasks Achieved:
-
Using the machinery's handbook to determine the tolerances of a part needed to achieve fits specified by the other team members Fits table in the final report
-
Using the machinery's handbook to determine the grade and compatibility of a manufacturing process based on the specified fits by other team members in the Fits table in the final report
-
Double-checking the grades list checking for the working drawings document with our working drawings
-
Writing the differentiation section for how our clampable desk organizer in the final report
-
Writing the justification of the manufacturing process selection, design for manufacturing, and material choice section of the final report
Operating a Lathe and Mill to Manually Machined an Aluminum Widget


I had the opportunity to use UC Berkeley's machine shop to learn the basics of using a lathe, mill, and drill press.
Skills Learned
-
Using a Lathe
-
Using a Mill
-
Using a Drill Press
-
Learning safety habits for soft and hard metals
-
Finding an edge with an edge finder
-
Manually zeroing my coordinate system
-
Cleaning the environment for the next person
Things I Learned By Experience | Creating furniture, a shed, and more DIY
The following lists all the habits, safety procedures, and skills I learned by creating stuff.
Many of the things I listed are from working on DIY projects with my dad: creating furniture, a shed, repairing rotten wood for a deck, building scaffolding to repair the sidings of our house, etc.
Using Power Tools and Traditional Construction Tools
-
considering the thickness of a saw blade
-
pushing in the screwdriver or drill bit into a screw to prevent destroying of the bit hole
-
considering the kickback of a saw blade as you cut a 2 by 4 piece of wood, and holding the wood with your hand to prevent this
-
Also allowing the saw blade to have full motion when cutting the wood instead of having the blade stop in the middle, inducing kick back
-
having eye protection to avoid overblinking if saw dust flies in my eyes
-
having a vaccuum to clear away saw dust or having to blow away the saw dust
-
using push blocks when dealing with saws to avoid getting my fingers chopped up
-
being aware of the direction a manual saw is designed to cut in
Assembling
-
Attaching all of the objects loosely first to be able to adjust pieces if necessary. Then, tightening pieces together
-
Pushing in screw driver or powerdrill into the drill hole to prevent jumping of the drill bit
Using 3D Printers and Laser Cutters
-
considering the flatness of a 3D printer bed and calibration
-
considering the mm thickness of the filament
-
considering the size of the baseplate and the height the printer provides
-
considering the time saved when using vector lines instead of raster lines for laser cutting
Machining Metals
-
when machining tough metals, using a lower gear ratio
-
when machining metal, oiling the metal to have a cleaner tap
Soldering
-
tinning the soldering iron to have better heat transfer, leading to circuits not being microscopically burned. Also to prevent oxidation on the tip
-
Pulling the solder first, then the iron to prevent the solder from being stuck
-
Allowing the solder to geep between the connection point of the component
-
using a putty or plado to hold the wires flat on the table
-
using a fan to prevent fumes from going in my lungs
-
when stripping whires, using a wire stripper
-
wrapping wires around each other to cancel out magnetic fields comeing about wires